Pros of Galvalume® roofing
- Least expensive – Compared to other high-quality metal roofing materials, Galvalume costs the least amount of money. Depending upon the thickness, color and quality of the desired Galvalume panels, pricing ranges anywhere from $5.00 to $15.00 per square foot. Keep in mind that in 2021 and 2022, steel prices continually fluctuate and vary dramatically.
- Corrosion resistant – Galvalume’s chemical formula was specifically designed to combine the toughness, strength and self-healing properties of zinc with the rust-resisting properties of aluminum. That’s why Galvalume’s corrosion resistance is about two to four times better than galvanized steel. Galvalume’s self-healing characteristics help control the red rusting at any cut/exposed edges. Nearly all steel-based products will experience some level of normal edge creep from the exposed steel when the coil is cut, but it is minimal and will eventually stop with Galvalume. Remember that edge creep can also be offset by hemming the panels and touching up any exposed edges with paint pens.
- Easy to handle and install – Another benefit of Galvalume is that it’s not as temperamental as other metals used in the roofing industry, like copper and zinc. Installers don’t have to worry as much about leaving fingerprints, deep scratches, etc., on panels because Galvalume is tougher and a little more tolerable. It also doesn’t have many strict ventilation or air gap requirements like some other metals. Plus, Galvalume is a standard metal roofing product and doesn’t have too many special requirements, which allows the installation details to be pretty standard across the board. Even though it’s a tough material, installers still find Galvalume easy to handle, rollform, cut and beyond.
- Warranties – One of the number one selling points of Galvalume is the 25.5-year warranty on the substrate, which is sometimes referred to as a perforation warranty. Galvalume systems also often come with paint warranties that further protect your investment and provide peace of mind that the roof or wall system will last (substrate or paint warranties are NOT available for Galvalume products within 1,500 feet of a coast). Plus, commercial property owners can buy a weathertight warranty for their Galvalume roofing structure, which ensures the roof was installed correctly and adheres to strict installation details.
Cons of Galvalume® roofing
- Oil canning – Oil canning is an inherent characteristic of light-gauge, cold-formed metal products, especially products with broad flat areas. It is a visual phenomenon seen as waviness or distortion in the flat surfaces of metal walls and roofing products. Oil canning is subjective and normally only an aesthetic concern that does not affect a product’s strength or performance. This occurrence is possible for any kind of metal roofing or walls, including Galvalume. But there are methods to minimize the appearance of oil canning, including:
- Hiring an experienced contractor who knows the best methods to reduce oil canning, including:
- Panel thickness
- Appropriate space between panels
- Underlayment
- Deck or other supporting structure is in alignment
- Buying trustworthy brands of coil
- Using striations or bead stiffeners in the flat area of the panel to minimize the appearance of oil canning
- Not suitable for animal enclosures or buildings – Galvalume is not suitable for use on buildings where animals are housed or held. Manure from the animals breaks down into ammonia gas over time and then reacts with the Galvalume coating. This process breaks down the Galvalume coating and leads to the degradation of the metal. However, Galvalume is sometimes used on modern chicken houses built with a vapor barrier between the chicken area and the roof for appropriate ventilation. It’s best to check with the manufacturer before putting Galvalume on an animal confinement building, as it’s often dependent on the specific design and use.
- Interactions with other materials – Combining different metals on a metal roof system can lead to interactions that could result in early degradation, staining and potential failure of a system altogether. Galvalume performs best when not in contact with copper, lead, bricks, treated lumber, iron and concrete. If Galvalume is in contact with one of these and is then introduced to an electrolyte such as water, it can lead to galvanic corrosion of the metal.
Learn more about Galvalume® metal roofing
2 - Aluminum metal roofing
Aluminum is a lightweight, silver-white metal that is element 13 on the periodic table and is the third most abundant element on Earth. However, aluminum never occurs in its metallic form in nature. Its compounds, usually aluminum sulfates, are chemically broken-down using electrolysis/electrolytic reduction to produce the aluminum metal material.
Overall, aluminum is suitable as a roof, wall, trim, and more in several different environments, including coastal environments, hurricane zones, locations with high rain or snowfall, high-temperature regions and more.
Pros of aluminum roofing
- Suitable for use in coastal environments – One of the most significant benefits of aluminum is that it can be installed in coastal environments. Aluminum has much better corrosion resistance than steel products, especially in harsh coastal environments where saltwater can wreak havoc on a metal roofing system. Because aluminum oxidizes as it starts to corrode, it actually makes it stronger and prolongs the life of the system on the coast. Best of all, aluminum roofing systems still carry a PVDF paint warranty when installed in coastal areas.
- Warrantied product – Aluminum metal roofs come with a variety of warranty options, including paint, substrate and weathertight warranties, which help to protect your investment and provide peace of mind that the roof or wall system will last. There are even paint warranties on aluminum sheets/coils used in coastal applications. For example, Sheffield Metals offers a 25-year PVDF paint warranty for coastal properties and a 20-year PVDF paint warranty for Caribbean properties. Plus, commercial property owners can buy a weathertight warranty for their aluminum roofing structure. Learn more about Sheffield Metals’ weathertight warranties in this comprehensive article.
- Self-healing and no red rust – Aluminum is unique in how it handles the minimal corrosion it experiences. When it does corrode, it doesn’t red rust as steel does; instead, it oxides and forms hard oxidation (or oxide film) on its coating, which protects the aluminum. This helps to preserve the metal and make it last in very corrosive environments, like coastlines. Plus, the oxidation forms rather quickly, so there’s no edge creep that eats up the panel like a steel substrate with red rust.
- Lightweight and strong – Aluminum is one of the lightest metal materials, especially compared to steel products. When you compare gauges and thicknesses on a weight-per-square-foot basis, 24-gauge Galvalume typically measures as .023” or .024” in thickness. The comparable aluminum thickness is .032” (equivalent to 24-gauge Galvalume in strength), so the aluminum is thicker but only half the weight. A typical 24-gauge Galvalume roof weighs anywhere from 1 to 1.5 pounds per square foot, and a .032 aluminum roof weighs less than 0.5 pounds per square foot. The lightweight properties of aluminum make it easier for contractors/installers to transport, handle, rollform and get panels onto the roof deck.
- Highly recyclable – Metal is almost always recyclable in one way or another, and aluminum is one of the most reusable and sustainable metals in the world. For reference, about 95% of all aluminum roofing systems installed worldwide are made from previously recycled aluminum materials. At Sheffield Metals, we use a 3000 series aluminum alloy (3105) primarily made from previously recycled materials and very little pure aluminum.
Cons of aluminum roofing
Medium-high price point – Aluminum is in the mid to high price range for material cost, which makes it a more expensive metal material option. Aluminum standing seam metal roofs come in at about $7 to $18 per square foot depending on thickness, finish, profile, location, installer and many other factors.
Denting concerns – Aluminum is more malleable than steel, which means it can be bent and manipulated much more easily and won’t suffer breaks or cracks. However, it has also been known to dent easier than other metals during and after the installation. Contractors should be extra careful when handling and installing aluminum materials/panels. Additionally, if a structure is beneath trees or other objects that could fall on the roof, another type of metal material may be a better option to help preserve the roof’s aesthetic. Luckily, the tensile strength of aluminum is comparable to steel, but aluminum is more susceptible to surface denting.
Requires more space for thermal movement – Aluminum expands and contracts roughly twice as much as a steel roof. This is something that contractors need to be aware of during the installation to allow enough room for the thermal movement of the panels. This is especially important when using a mechanically seamed panel in lengths greater than 15-20 feet. For panels this length, it’s recommended that an expansion clip be used per the applicable engineering. Restricted expansion and contraction of an aluminum roof can cause oil canning, increased noise and more required maintenance on any exposed fasteners.
Natural color – Using a bare aluminum product with its original natural silver-gray color isn’t usually recommended. As the metal ages, experiences weathering and oxidizes (white rust), it doesn’t hold its original mill-finished color and often becomes washed out and spotty. The best way to overcome this issue is to buy painted roofing coils or panels, which will age much cleaner over time because the paint covers any of the metal color changes.
Learn more about aluminum metal roofing
3 - Zinc metal roofing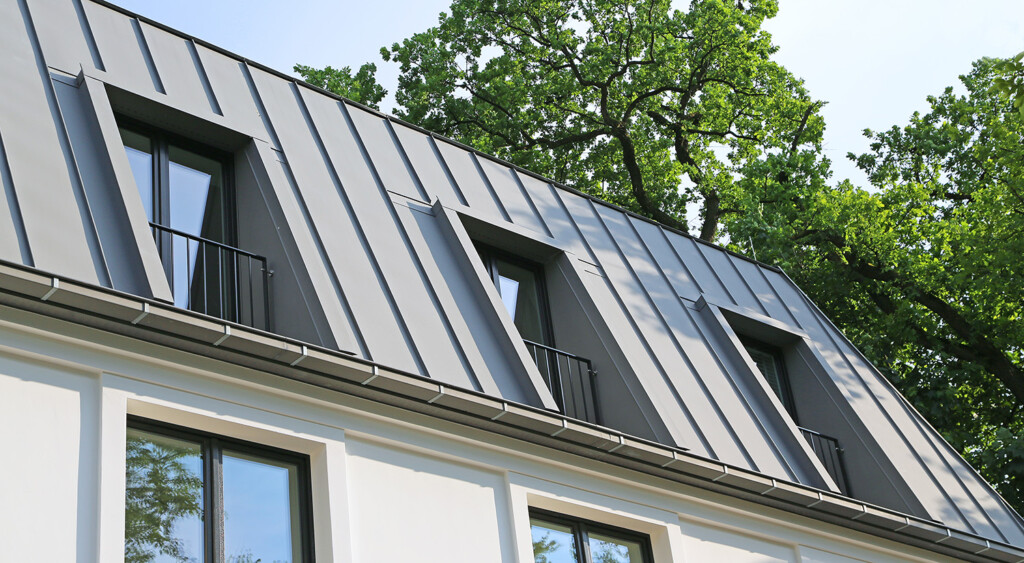
Zinc is a lustrous bluish-white metal and is the 24th most abundant element in the Earth’s crust. According to geogly.com, zinc is currently the fourth most widely consumed metal in the world after iron, aluminum and copper. Zinc is a material option that is relatively common in the standing seam metal roofing industry in Europe and is gaining popularity in the US, as it’s designed to withstand the elements, has self-healing characteristics and is environmentally friendly.
Pros of zinc roofing
- Longevity – Zinc roofs have been known to last anywhere from 60 to 100 years. Studies have shown that zinc roofing could sometimes last up to 150 years, depending on the quality of installation, building properties and climate.
- Ecofriendly – Since zinc is a natural metal extracted from the ground, zinc’s toxicity levels are low, even after fabrication. Homeowners and business owners do not have to worry about toxic run-off or ground pollution surrounding their zinc roofing. Additionally, zinc is a non-ferrous metal, meaning it does not contain iron and therefore requires less energy to manufacture.
- Self-healing characteristics – Zinc has an outer protective layer that prevents corrosion, scratching and other panel markings. If wind or another element were to scratch the surface of the zinc roof, the metal’s protective layer would fix and correct itself over time.
- Easy to form – Architects and contractors often use zinc in their projects because it’s a softer metal and can be easily shaped into different profiles for rollforming, gutter forming and seam creation.
- Limited warranty options – Zinc can come with some limited substrate warranty options. However, checking with your roofing material manufacturer is critical, as the warranty options will vary and often depend on specific environmental variables.
Cons of zinc roofing
- Expensive – The most prominent drawback to zinc roofing is the price. While many variables factor into the cost and prices continue to fluctuate dramatically into 2022, zinc roofing can cost anywhere from $650 to $1100 per roofing square (100 square feet).
- Underside corrosion – If the zinc roofing is improperly coated on the underside and water molecules get trapped underneath/between the panels and the insulation or underlayment, the zinc metal can corrode.
- Ventilation concerns – All zinc applications require adequate ventilation to help prevent the system from failing from the inside (or underside) out. Above deck ventilation products, such as Sharkskin Ventilated Mat or Enkamat, combined with using the appropriate installation details, will contribute to the longevity of a zinc system. The correct ventilation process for zinc roofing is more of a precaution than a disadvantage.
- Expansion and contraction concerns – In climates with striking temperature differences, zinc roofing often expands and contracts during heating and cooling cycles more than aluminum metal systems. Your contractor should ensure that your system can accommodate this thermal movement.
- Limited engineering options – There are limited uplift-tested options available for most types of zinc standing seam metal roofs. If you find one, it will most likely be a mechanical seam and not a snap-lock profile.
Learn more about zinc metal roofing
Comments
Leave a Reply
Have an account? Login to leave a comment!
Sign In